Our equipment
Air Compression
LMF 39/25 Air Compressor
LMF Portable Diesel Compressors are rugged in construction yet quiet in operation. The LGCY 39/25 can operate in both single stage or dual stage operation to provide either 1377 scfm @362 psi, or 1165 scfm @ 507 psi. Fitted with Cummins engines, performance and reliability are key factors setting the product apart in a very competitive market.
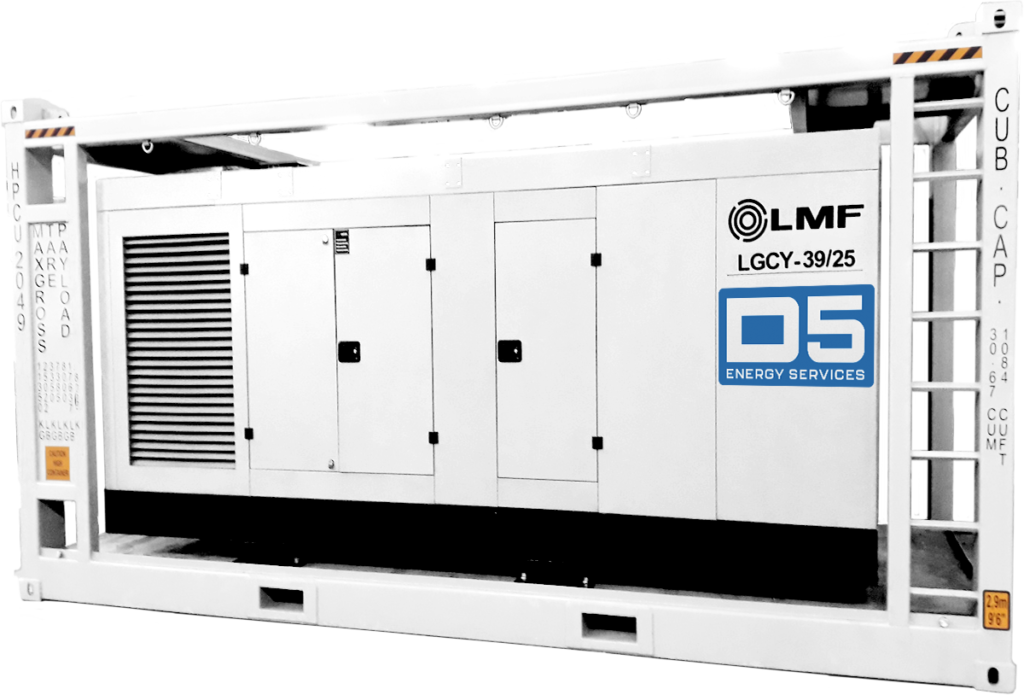
Medium & High Pressure Boosters
The D5 Energy Services range of booster compressors are constructed to safely compress air, natural gas or nitrogen and can be operated in either a single or double stage configuration. The WB12 Joy range shown here offers pressure capabilities up to 2500 psi and volumes to 3800 scfm.
A high pressure booster typically designates pressures in excess of 2500 psi, and practically up to about 5000 psi. Usually these are WB-11 or WB-12 “superbooster” units that can compress the outlet pressure of the medium pressure to the desired higher pressure. Other models that are in use include the Ariel JGA/4 models that can deliver about 2000 scfm of air/N2 to a pressure of up to 5000 psi.
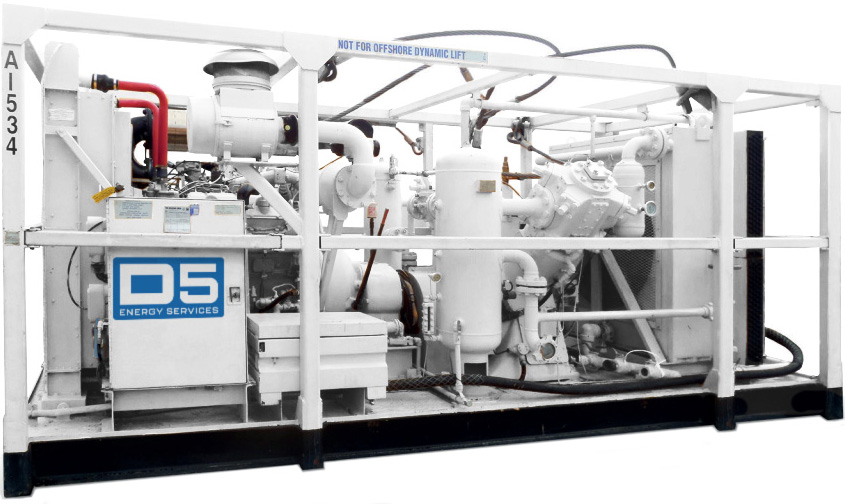
Membrane Nitrogen Generators
Membrane nitrogen modules contain over a million fibers. Compressed feed air is passed down the bores of the fibres at one end of the module, with enriched nitrogen product gas exiting from the opposite end. Oxygen and water vapour are selectively removed and vented from the feed air as it flows through the module.
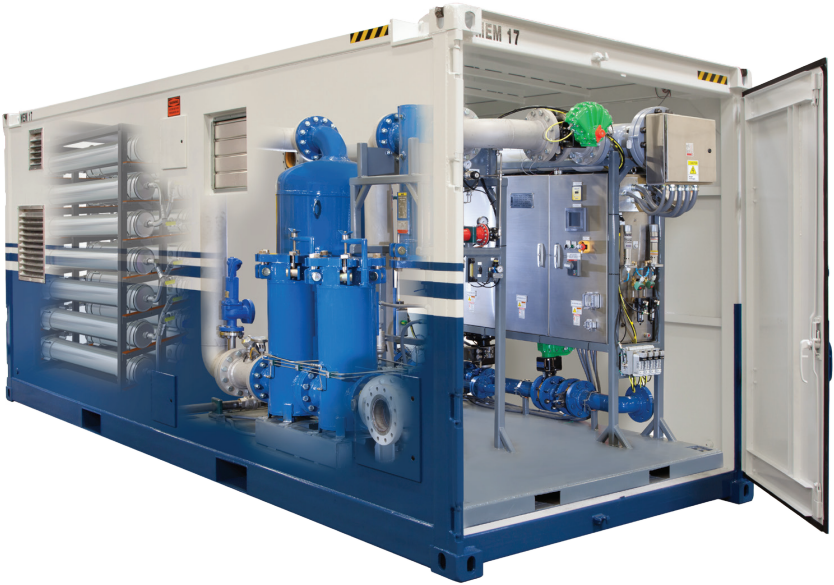
Advantages of membrane generated nitrogen over cryogenic
- Enhanced mobility and rapid deployment.
- Ideal for remote locations, offshore and onshore.
- No need to haul in liquid nitrogen or nitrogen tube trailers.
- No risk of running out of liquid nitrogen.
- Can produce purities from 92-99.9%.
- 50°F to +140°F (-45°C to +60°C)
- Nitrogen Dew Point down to – 700°F (-570°C)
- Hydrocarbon free
Continuous Circulation
D5 Energy Services continuous circulation system (CCS) enables continuous circulation during the drill pipe connection process for drilling, while tripping narrow pressure window wells and for providing continuous hole cleaning. By maintaining constant circulation of drilling fluid, operators can keep their rig pumps on while adding and removing drill pipe. With continuous circulation, there is no interruption to the flow of drilling fluid into the well throughout the process of adding drill pipe joints to—or removing these joints from—the drill string. This unique technology solves many potential problems; in particular, it helps maintain flow through continuous hole cleaning and solids transport.
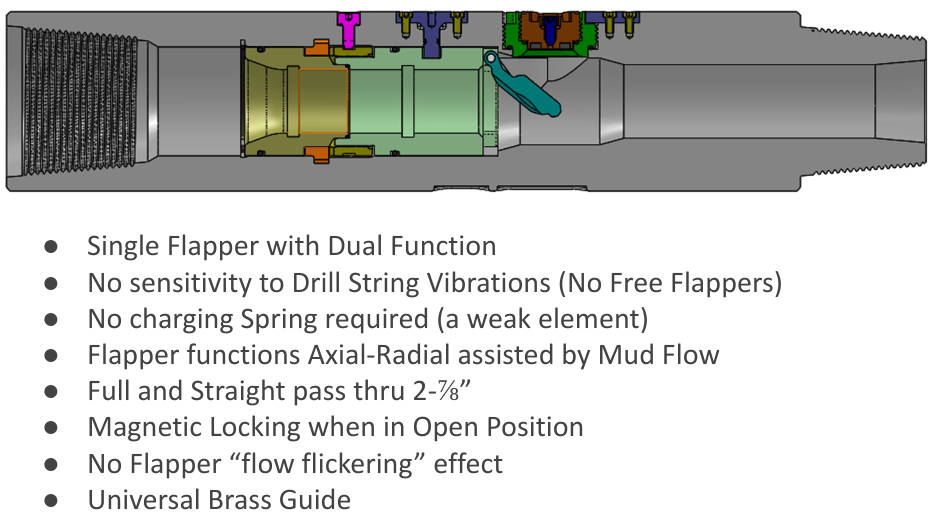
Casing Valves
Downhole Isolation Valve
The Downhole Isolation Valve (DIV) is run as an integral part of the well’s casing string. The valve is a surface controllable valve, which opens to the full bore of the casing to allow passage of the drill bit while the drill string is tripped in or out of the hole. Operation of the valve is achieved through the application of pressure via a hydraulic control line run through the annular space between two casing strings.
The DIV is used whenever the drill string is retrieved from the well, or whenever surface pressure exists when deploying the drill string into the well. When it is necessary to pull the drill string out of the hole, the drill string is tripped out until the bit is above the DIV. The DIV is then closed, and pressure above the valve is bled off so that the drill string can be safely removed from the hole. The drill string can then be tripped back into the well until the bit is just above the DIV. The DIV is then reopened, and the drill string is run in to continue the drilling operation.
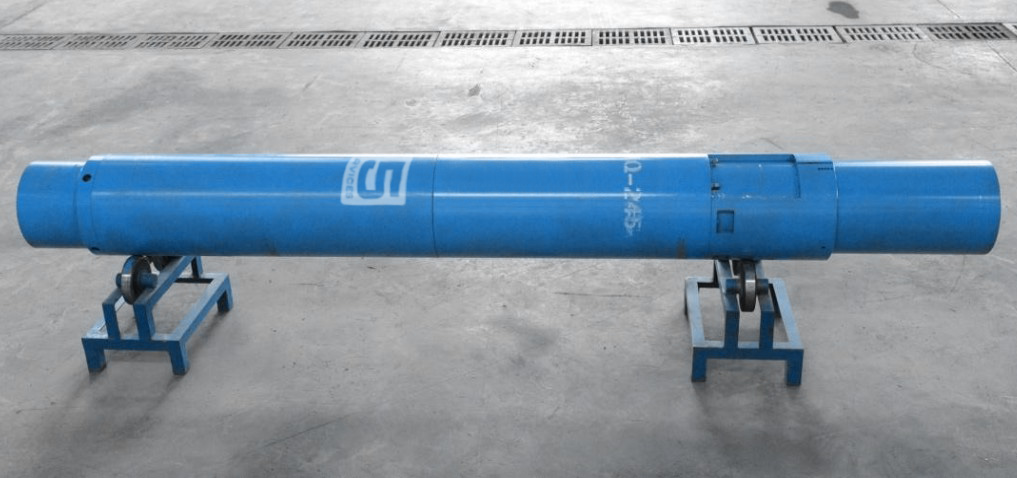
Rotating Control Devices
RCD-5000 for MPD & UBD
The D5 Energy Services RCD-5000 is a Dual rubber Rotating Control Device (RCD) which is designed with two sealing elements for added safety and performance. The upper and lower sealing elements can be easily and quickly changed so as to save time. Rotating assembly can be installed or removed with an integral piece so as to improve work efficiency. The D5 Energy Services RCD-5000 dual rubber Rotating Control Device (dual rubber RCD) is designed and manufactured in accordance with API16‐RCD.
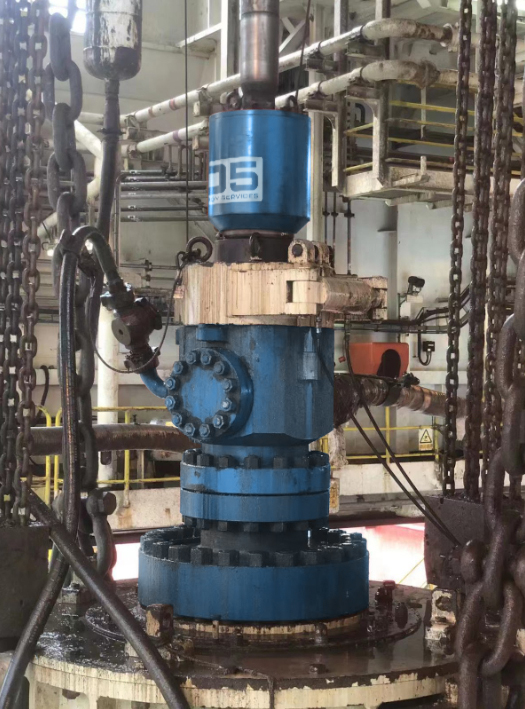
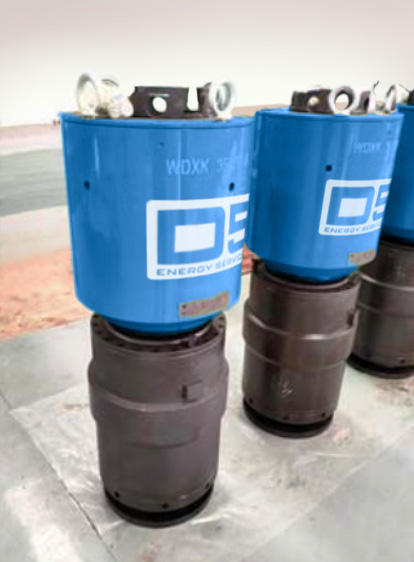
RCD-1500 for MPD & UBD
The D5 Energy Services RCD-1500 is a single rubber Rotating Control Device (RCD). The sealing element can be easily and quickly changed so as to save time. Rotating assembly can be installed or removed with an integral piece so as to improve work efficiency. The D5 Energy Services RCD-1500 single rubber Rotating Control Device is designed and manufactured in accordance with API16‐RCD.
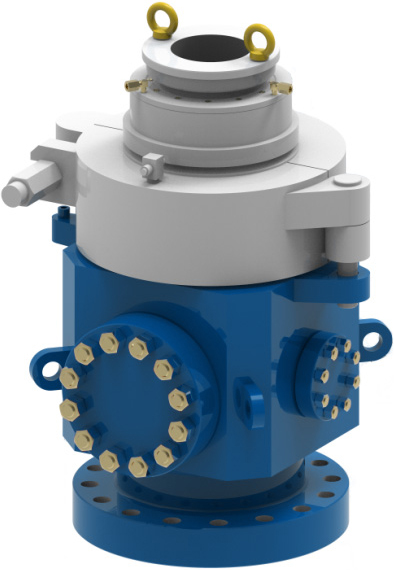
RCD’s for Air/Mist/Foam/Aerated Drilling
The D5 Energy Services RCD-600 is the original Rotating Control Head. This unit is designed to seal off the drill string components continuously and divert all cuttings and debris away from the rig. Designed for Top Head and for Kelly Drive rigs, these units can handle up to a 5 1⁄4” Hex and 4 1⁄2” Square.
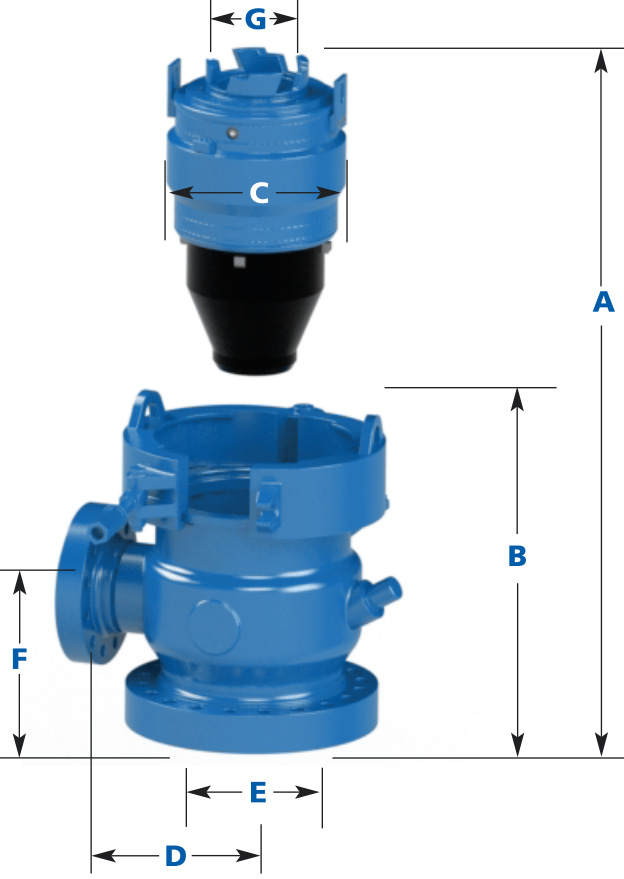
Managed Pressure Drilling System
- Compact automated MPD manifolds designed according to the following specifications:
- Maximum working pressure: 5,000 psi as per API 6A
- Range of working temperatures: -20 to 121 deg C as per API 6A
- Manifold service level: PSL2, NACE MR-0175 Sour Service
- ATEX zone 1 classification
Available in standard horizontal configuration and “ultra-low footprint” vertical configuration
- Main components:
- Dual redundant MPD chokes with electric actuator
- Integrated Coriolis Mass-Flow meter
- Isolation valves and bypass lines
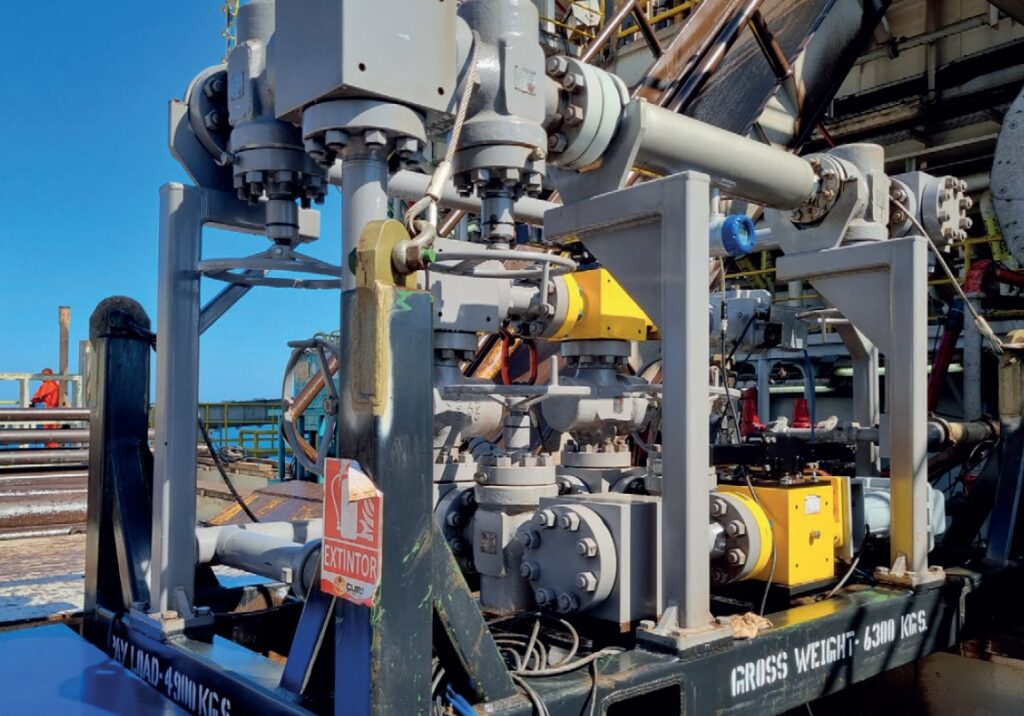
- Sensors and cable package
- Pressure relief valve
- Ultra-compact PLC control- and data acquisition system
D5 Energy Services focuses on compact and robust systems with a proven track record in managed pressure drilling. A cutting-edge proprietary automated control system is used in combination with robust fully redundant electrically actuated chokes and integrated flow measurement.
The control and data acquisition system incorporates a model-based algorithm capable of monitoring and responding in real-time to the dynamic drilling environment, downhole incidents, and sensor failures.
- Fully (auto-)coordinated choke control that can be operated in the following modes:
- Manual Position setpoint
- Automatic surface backpressure control
- Automatic Standpipe pressure control
- Automatic connection pressure control
- Automatic bottomhole pressure control with Hydraulics Model
- Single or dual choke control mode to minimize surface friction at high flow rates or in plugging events
Advanced MPD Modes:
Early Kick/Loss Detection and Control
- A proprietary model-based algorithm monitors the dynamic mass balance of the fluid in the well in real-time. Model-based compensation of compressibility allows detection of influx or loss both in transient and static conditions, and provides higher certainty of detection in flow transients, such as ramp up/down for connections, during tripping in or out of the well, and during pressure set-point changes in MPD operations.
- Benefits:
- Earlier detection of influx or losses
- Detection of false alarms
- Significant reduction of NPT caused by kick/loss events
Real-Time Hydraulics Model
- A robust real-time digital twin of the well with distributed multi fluid transients and pressure and flow dynamics. The model enables fully automatic constant bottomhole pressure by selecting an Equivalent Mud Weight setpoint at a specified anchor point in the wellbore.
- Key capabilities:
- Real fluid PVT and rheology models
- Cuttings distribution and transport
- Multi-fluid operations; mud rollover, cementing, front tracking and visualization
- Continuous mud weight changes
- Surge/Swab calculations, with tripping speed limits
Underbalanced Drilling System
Typically during underbalanced drilling (UBD) the drilling fluid will need to be lightened by injecting air, natural gas or on-site generated nitrogen. This is done by using membrane nitrogen separation equipment which can deliver virtually any volume of high (95-99%) purity nitrogen at pressures up to 340 bar/5000 psi. Then downstream of the well is the UBD choke and separation system that controls and separates the return flow of gas, liquid hydrocarbons, drilling mud and cuttings. The oil and/or gas can be sent to an export pipeline or process facility, storage tanks, or a special burner. The drilling mud can be recirculated and drilled cuttings are sent to the shakers or confined storage.